top of page
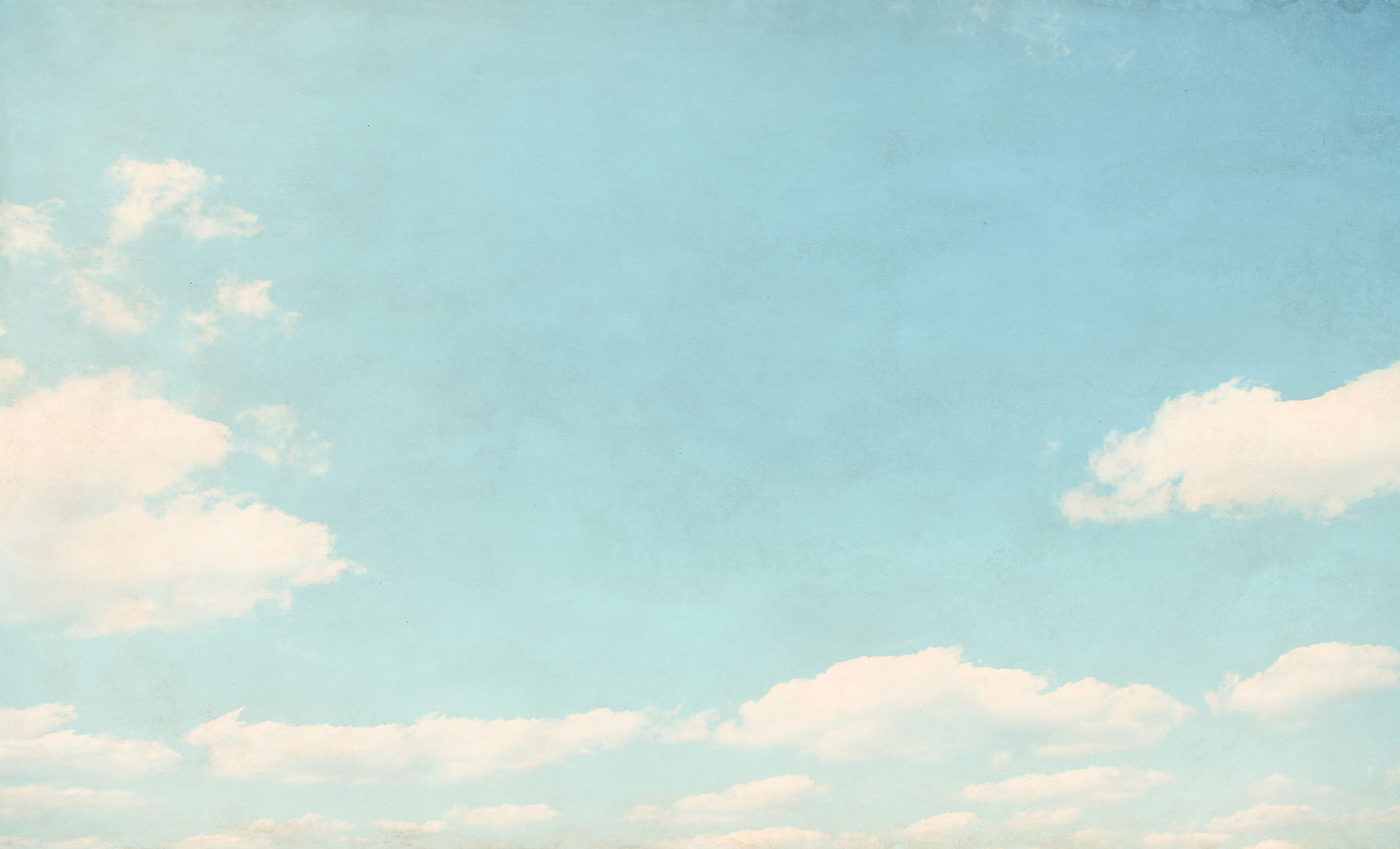
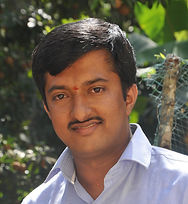
Dr. Vishnumurthy K A
UNIT V
​
POLYMERIC MATERIALS
A polymer is a macromolecule having high molecular mass more than 10,000. Formation of such molecule requires combination of large number of small molecules. Such small molecules are called monomers and they should possess at least two functional groups or unsaturated bonds that can combine with similar or different type of simple molecules. The process involved in combining of monomers to get a polymer is called polymerisation. The number of times the monomer units repeat in a polymer is called degree of polymerisation.
Classification of polymers:
Polymers are classified in following ways.
1. Based on method of polymerisation: Addition polymers and Condensation polymers.
2. Based on effect of heat: Thermoplastic and thermosetting polymers
3. Based on the way of repeating units linked: Linear, branched and cross linked polymers.
4. Based on origin: Natural and Synthetic polymers.
5. Based on arrangement of molecules: Crystalline and amorphous polymers.
Methods of Polymerization
To carryout polymerization in a test tube or small flask may be difficult. However, problems are encountered when the process is scaled up to industrial level (large scale production). The problems like increase in temperature due to exothermicity of the reaction and very high increase in viscosity are most common. It is also expected that the products obtained must be able to serve the purpose (as fibre, adhesive, plastic, foam, and rubber.etc.) without much purification Manufacturing techniques can be classified into following types based on the conditions maintained.
Bulk polymerization
It is the simplest technique. The monomer in liquid form and an
initiator soluble in liquid monomer are taken in a reactor. This
forms a homogeneous system. The reaction is initiated by heat or
photo chemically. As free radical polymerizations are exothermic
heating need not be continued. Instead excess heat liberated has
to be taken out. Almost the whole of the monomer (bulk) gets
converted into polymer.
​
The advantages of this technique are:
(i) Product obtained will be pure as no other substance other than initiator is added.
(ii) Product will have good optical clarity as no impurities exist.
(iii) Percentage conversion is almost hundred
(iv) The method is simple and needs simple equipments.
(v) Polymer recovery is easy
​
​
Disadvantages of the process are:
(i) As the polymerization progresses, viscosity of the material increases. This makes it difficult to stir the product.
(ii) The reactions are exothermic. So lot of heat is generated. Unless heat is removed, there is a chance of explosion and degradation of polymer.
(iii) Temperature control is difficult due to viscosity increase. Heat cannot be extracted out easily as stirring becomes difficult. Low thermal conductivity and specific heat of the polymer add to the problem.
(iv) As the movement of the molecules gets restricted due to viscosity increase, rate of termination decreases. Growth propagation of large number of chains to the site of monomers leads to hot spot formation again leading to decomposition of the polymer.
(v) The polymer obtained will not have good molecular weight distribution as chain growth will not occur uniformly, throughout the bulk. Polymers like polystyrene, poly (methyl methacrylate), low density polyethylene and many condensation polymers are prepared by this method.
Suspension polymerization
In this process monomer is suspended in water as droplets
(50-diameter). An initiator soluble in monomer is added.
So each of the droplets contains
monomer and the initiator (similar to bulk polymerization).
A chain- transfer agent is added to control the molecular weight
of the polymer. The droplets show a tendency to coalesce
(like oil in water). This is prevented by:
(a) Addition of a protective colloid like poly vinyl alcohol And
(b) Constant agitation (stirring) of the mixture. The mixture
is heated to about 600C. The droplets harden as polymerization progresses to
give beads. Each droplet acts as a miniature reactor and polymerises as in bulk polymerization.
​
​
The advantages of the processes are :
(i) Heat transfer is efficient as water having high specific heat forms the continuous phase.
(ii) Agitation or stirring is easy due to negligible viscosity build up.
(iii)It is economical as solvent (water) cost is low.
(iv) Polymer (which is in the form of beads) can be easily recovered by a simple filtration
and then washing.
The disadvantages of the process are:
(i) Polymer obtained is not pure. It is contaminated by additives like protective colloids.
(ii) Reactor cost is relatively high. Polystyrene, polymethyl methacrylate, poly vinyl chloride ,polyacrylonitrile etc. are prepared by this technique.
Emulsion polymerization
Dispersion of a liquid in another liquid that are immiscible is called emulsion. In this process a liquid monomer is emulsified in water and the emulsion is stabilized by adding soap or detergent (emulsifying agent). A water soluble initiator (in suspension polymerization initiator is monomer soluble) and a chin transfer agent are added. The monomer droplets are very much smaller (typically 0.5 micro meter ) when compared to suspension polymerization polymerization.
Solution polymerization
In this method monomer and initiator are dissolved in a suitable
solvent to form a solution. So it is polymerization in homogeneous
condition. The solution is heated to start polymerization.
The solvent selected should have suitable boiling point and
chain transfer characteristics. After the reaction is over solvent
is removed to get the polymer. Important organic solvents used
are aliphatic and aromatic hydrocarbons, esters, ethers and alcohols.
The advantages of the process are:
(i) Because of the presence of solvent, the viscosity build up is low. This makes stirring easy
and reduces the chances of hot spot formation and explosion.
(ii) As stirring is easy, heat transfer is effective.
(iii)The paste (of polymer in the solvent) can be directly used as an adhesive and in paints.
The disadvantages of the process are:
(i) Yields will be less due to the presence of large of the solvent.
(ii) Product will be impure as removal of last traces of solvent is difficult.
(iii)There is a need to recover the solvent. Therefore the technique requires a separate
solvent recovery unit.
(iv) Costly solvent increases the cost of the process.
(v) High molecular weight products cannot be obtained as solvent acts as a chain transfer agent this increases the possibility of termination.
Polystyrene, polyvinyl chloride (PVC) poly butadiene polyacrylamide etc. are prepared by this technique.
Glass transition temperature
The temperature at which a polymer transforms from stiff, hard, glossy state to
rubbery state is called glass transition temperature (Tg). The temperature at which
the polymer melts and starts flowing is called flow temperature. (Tf or Tm).
SIGNIFICANCE OF Tg
i) It is used as a measure for evaluating the flexibility of a polymer and the type of
response the polymeric material would exhibit to mechanical stress.
ii) Tg is very useful in choosing the right processing temperature for fabrication
(molding,calendering and extrusion)
iii) Tg is very useful in determining the coefficient of thermal expansion,
heat resistant refractive index, electrical property etc.
Synthesis of poly carbonate
Polycarbonates are the polyesters of unstable carboxylic acids. They contain [-O-COO-] linkage through the chain. Polycarbonates are prepared
by condensation of (i) Posgene and sodium salt of Bis-phenol-A (ii) Diphenyl carbonate and Bis-phenol-A
Properties:
1. It has high tensile strength and impact resistance.
2. It is white transparent thermoplastic polymer.
3. Highly soluble in alkalies and acids
4. Got very high melting point.
​
​
​
Applications:
1. Used in the manufacture of many useful articles such as telephone parts, unbreackable glazing appliences, etc due to its high tensile strength.
2. Used in the manufacture of safety goggles, automobile lenses, DVD, CD etc due to its transparent nature.
Acrylonitrile butadiene styrene (ABS)
The monomers used in the synthesis of ABS are, acrylonitrile, butadiene and styrene
Properties:
(i) Very strong having very high impact resistance
(ii) High thermal and chemical resistance.
(iii) Provides glossy surface.
​
​
​
​
THERMOSETTING POLYMERS:
Some polymers, on the other hand, undergo some chemical change on heating and convert themselves into an infusible mass. They are like the yolk of egg, which on heating sets into a mass, and, once set, cannot be reshaped. Such polymers, that become infusible and they are called as thermo setting polymer
Properties:
1. Epoxy resins possess good electrical insulating properties.
2. Epoxy resins are resistant to water, acids, alkalis and various organic solvents.
3. They offer very good wearing and abrasion resistance.
4. The polar nature of the resins makes them excellent adhesives.
5. Cross linked polymers have high toughness and heat resistant properties.
Applications:
1. It is used as an adhesive to bind wood, glass, concrete, ceramic, metallic and leather
materials.
2. Epoxy resins are applied over cotton, rayon and bleached fabrics to impart grease
resistance and shrinkage control.
3. Used in manufacture of skid resistant industrial floorings and highway surfacing.
4. Used as laminating materials for electrical equipments.
5. Moulds which are made from epoxy resins are used in the production of aircraft and
automobile components.
Note: Curing of epoxy resins
Epoxy resins are converted in to three dimensional cross linked polymers by reaction with
curing agents such as polyamides, polyamines, dicarboxylic acids, acid anhydrides, etc. The
process is called curing of epoxy resins. On curing epoxy resins show outstanding properties
of toughfness, chemical inertness, flexibility and strong adhesion.
(Araldite)
These are the polymers contain epoxy group on both the ends. The most common epoxy resin is obtained by condensation reaction of epichlorohydrin and Bis-phenol-A in the presence of NaOH as catalyst.
Properties:
1. Epoxy resins possess good electrical insulating properties.
2. Epoxy resins are resistant to water, acids, alkalis and various organic solvents.
3. They offer very good wearing and abrasion resistance.
4. The polar nature of the resins makes them excellent adhesives.
5. Cross linked polymers have high toughness and heat resistant properties. Applications:
1. It is used as an adhesive to bind wood, glass, concrete, ceramic, metallic and leather materials.
2. Epoxy resins are applied over cotton, rayon and bleached fabrics to impart grease resistance and shrinkage control.
3. Used in manufacture of skid resistant industrial floorings and highway surfacing.
4. Used as laminating materials for electrical equipments.
5. Moulds which are made from epoxy resins are used in the production of aircraft and automobile components. Note: Curing of epoxy resins
Epoxy resins are converted in to three dimensional cross linked polymers by reaction with curing agents such as polyamides, polyamines, dicarboxylic acids, acid anhydrides, etc. The process is called curing of epoxy resins. On curing epoxy resins show outstanding properties of toughfness, chemical inertness, flexibility and strong adhesion.
Phenol Formaldehyde resins:
Phenol-Formaldehede (PF) resins are formed by the poly condensation
between phenol and formaldehyde. The polycondensation reaction can be
catalysed either acids or bases.
Synthesis:
Aqueous solution of formaldehyde with phenol is heated to 70-75 C.
The monomers like monomethylol phenol, dimethylol phenol, trimethylol phenol are formed.
These monomers condense to give a polymer.
The nature of the reaction depends on the ratio of phenol to formaldehyde in the solution.
BIODEGRADABLE POLYMERS:
It is observed that plastic bucket kept in sunlight and rain for long time loses its lustre constitution of the polymer. Conventionally, the degradation is a reduction in the molecular weight of the polymer. In developing countries, environmental pollution by synthetic polymers has assumed dangerous proportions. Petroleum-derived plastics are not readily biodegradable and because of their resistance to microbial degradation, they accumulate in the environment. In addition in recent times oil prices have increased markedly. These facts have helped to stimulate interest in biodegradable polymers. Biodegradable plastics and polymers were first introduced in 1980s. Polymers from renewable resources have attracted an increasing amount
of attention over the last two decades, predominantly due to two major reasons: firstly environmental concerns, and secondly the realization that our petroleum resources are finite. There are many sources of biodegradable plastics, from synthetic to natural polymers. Natural polymers are available in large quantities from renewable sources, while synthetic polymers are produced from non-renewable petroleum resources. Biodegradation of polymeric biomaterials involves cleavage of hydrolytically or enzymatically sensitive bonds in the polymer leading to polymer erosion. A vast number of biodegradable polymers have been synthesized recently and some microorganisms and enzymes capable of degrading them have been identified.
Requirements of Biodegradable polymers:
1. Biodegradable polymers should have hydrolysable linkages like esters, amides or ether.
2. They should be hygroscopic in nature.
3. The product formed after degradation should act as compost.
​
​
​
​
​
​
​
​
​
​
​
​
​
Conducting polymers
​
​
​
Photo conducting polymers
SYNTHETIC FIBRES
CARBON FIBERS
Carbon fibers are novel high-performance materials. They could be described as fibers containing at least 90 % carbon obtained by the controlled pyrolysis of appropriate fibers. Carbon atoms are bonded together in a crystal that are aligned parallel to the axis of fibre.. This alignment gives fibre high strength to volume ratio.Several thousand carbon fibres are bundled together which are then woven into fabric. Edison in 1879 found that carbon fibers can be used as carbon filaments in electric lamps. Since the early work of Edison, the carbon fibers have been investigated and used intensively
because they generally have excellent tensile properties, low densities, high thermal and chemical stabilities in the absence of oxidizing agents, good thermal and electrical conductivities, and excellent creep resistance. In recent years, the carbon fiber industry has been growing steadily to meet the demands arising from different applications such as aerospace (aircraft and space systems), military, turbine blades, construction, lightweight cylinders and pressure vessels, medical, automobile, and sporting goods. Furthermore, in the case of the carbon fibers, the range of their applications would depend on the type of precursors used to produce the carbon fibers. Consequently, many types of precursors have been studied to produce the carbon fibers. Carbon fibre from Poly Acrylo Nitrile (PAN) PAN-based polymers are the optimum precursors for the carbon fibers owing to a
combination of tensile and compressive properties as well as the carbon yield. The PANbased fibers were first developed by Dupont in the 1940s for use in the textile fiber. The thermal stability of PAN-based fibers was an important factor in expanding the application of fibers.
​
​
​
​
​
​
​
​
​
​
​
​
​
​
bottom of page