top of page
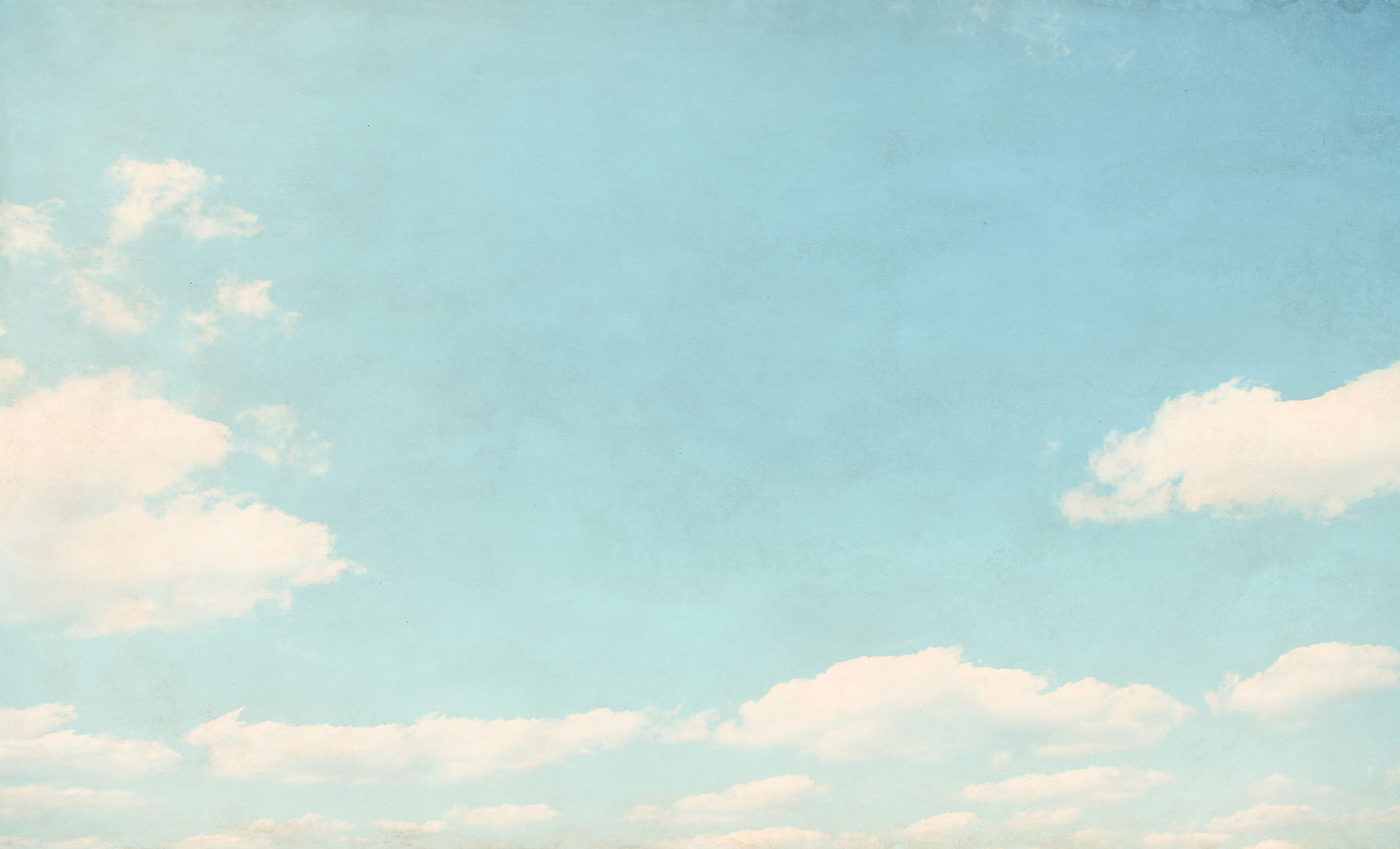
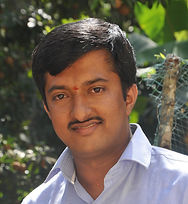
Dr. Vishnumurthy K A
UNIT III
CORROSION AND ITS CONTROL
CORROSION SCIENCE AND CONTROL
Corrosion can be viewed as a universal phenomenon. It is there everywhere, air, water, soil and in every environment, we encounter. There is no single figure for loss to the nation due to o corrosion could be around Rs. 2.0 lakh crores per annum in India. Corrosion costs manifest in the form of premature deterioration or failure necessitating maintenance, repairs and replacement of damaged parts.
Definition:
It is defined as the destruction or deterioration and consequent loss of metals due to chemical or electrochemical attack on its surface by the environment.
OR
It is a process where a pure metal or alloy is transformed from its metallic state to the undesired combined state due to interaction with the environment through chemical or electrochemical attack
Effect of corrosion:
1. Loss of metal: The loss of metal due to corrosion as Rs.20000 crores per annum all over the world.
2. Loss of useful properties of metal and result in loss of efficiency.
3. Maintenance and production cost increases.
4. Appearance: On rusting, reduced value of goods due to poor impression on the observer.
5. Contamination of products stored in storage tanks due to chemical reactions.
6. Loss of valuable products: The loss of uranium compounds is dangerous to environment.
7. While handling hazardous materials such as Conc.HCl, Conc.HNO3, explosive, the use of construction materials that minimize the corrosion failures
Reason behind corrosion
Metals are thermodynamically unstable. Naturally, metals are present in the form of metallic compounds (oxidized form) in their ores. During extraction, lot of energy is put into reduce metal ions to metal atoms. Hence, metals are always at higher energy state and are thermodynamically unstable. So metals are tried to come back to its originally state
Wet Corrosion (Atmospheric corrosion) (electrochemical theory)
It is common type of corrosion of metal in aqueous corrosion environment. It occurs when a liquid is present. This usually involves aqueous solutions or electrolytes and accounts for the greatest amount of corrosion by far
​
​
​
​
​
​
​
Types of corrosion
1)Differential metal corrosion/Galvanic Corrosion (galvanic corrosion)
This type of corrosion occurs when, two dissimilar metals are in contact and
jointly exposed to corrosive atmosphere. The metal with lower reduction potential
(anode) undergoes oxidation and the metal with higher electrode potential
(cathode) undergoes reduction. The potential difference between the metals
causes driving force for corrosion. The greater the electrode potential difference,
the higher is the corrosion rate. Thus anodic area always undergoes corrosion and
cathodic area remains unaffected. The anodic metal undergoes oxidation
and gets corroded. A reduction reaction occurs at the cathodic metal.
The cathodic metal does not undergo corrosion
2)Differential aeration corrosion:
This type of corrosion occurs when two different parts of the same metal are exposed to different oxygen concentrations. (Ex., An iron rod partially
dipped in water.) The part of the metal which is exposed to less oxygen concentration acts as anode. The part which is exposed to more oxygen concentration acts as cathode. The anodic region undergoes corrosion and the cathodic region is unaffected
Pitting corrosion
This is a case of differential aeration corrosion.When a small dust particle gets deposited on a steel surface, the region below the dust particle is
exposed to less oxygen compared to the remaining part. As a result, the region below the dust particle acts as anode undergoes corrosion and forms a pit. The remaining region of the metal acts as cathode and is unaffected
​
​
​
​
​
​
​
​
​
Corrosion control
(I) Protective coating, (II) Cathodic protection and (III) Corrosion Inhibitors
​
​
​
​
​
​
Impressed current method
​
Galvanizing: Galvanizing is the process of coating a metal surface such as iron with zinc metal. Galvanizing of iron is an example of anodic metal coating on the surface of a cathodic metal. Galvanization is carried out by hot dipping method. It involves the following steps.
1. The metal surface is washed with organic solvents to remove organic matter on the surface.
2. Rust is removed by washing with dilute sulphuric acid(Pickling)
3. Finally, the article is washed with water and air-dried.
4. The article is then dipped in a bath of molten zinc. (Molten zinc is covered with a flux of
ammonium chloride to prevent the oxidation of molten zinc.)
hot dipping galvanizing process
​
​
​
​
​
Electroless plating:-
Electroless plating is the controlled autocatalytic deposition of a continuous film of a metal from its salt solution by a reducing agent without using electrical energy. Electroless plating can be used for special applications for which conventional electrode position processes are unsuitable.
Advantages of electroless plating:-
.
1. Deposition on non conductors Ex., plastics is possible.
2. The baths have excellent throwing power - can be plated inside the tubes, recesses, etc.The hydrogen gas liberated is not in blind holes.
3. Excellent corrosion resistance.
4. Electroless coatings are harder than conventional electroplated articles and as a result resistance is increased.
5. No levelling is increased.
6 The deposits have unique chemical, mechanical and magnetic.
Electroless plating of Cu-Fabrication of PCB
Modern electroless copper films have a ductility and conductivity identical to that to that of electrolytic copper. The major technique used to plate copper on PCBs (i.e., to manufacture PCBs) is the substractive method. Printed circuit boards are composed of epoxides, phenolics, flexible films of polyester and polyimide. Copper foil is laminated to both sides of a flat board. Through holes are punched or drilled. The article (i.e., board) is first treated with organic solvents and alkaline solutions to remove grease and then etched in an acid. It is then activated by a specialised process i.e., dipping first in SnCl2 and then in PdCl2 solutions. It is placed in a electroless copper bath when a thin conductive layer of copper deposits on the entire board including the non conducting holes.
​
​
​
​
​
​
​
Why Fecl3 with HCl is used as etching agent:
It is used as PCB etchant in electronics and the hydrated form, FeCl3.6H2O. FeCl3 can act as an etchant, because of two reasons:
Fe(3+) is a fairly strong oxidizer.
Cl(-) is a strong complexing agent for copper (II) ions.
The reaction in solution often is written as
2Fe(3+) + Cu --> 2Fe(2+) + Cu(2+)
If you put copper in a solution of iron (III) sulfate then it does not dissolve. The chloride plays an essential role: 2Fe(3+) + Cu + 4Cl(-) --> 2Fe(2+) + CuCl4(2-)
In reality even this is simplified, because iron also is present as complex with chloride. So, a slightly better description of the reaction may be
2FeCl4(-) + Cu --> 2Fe(2+) + CuCl4(2-) + 4Cl(-)
When all iron (III) is converted to iron ()II), then the CuCl4(2-) ion in turn also oxidizes copper metal quite well, where copper (I) species are formed:
CuCl4(2-) + Cu --> 2CuCl2(-)
These copper (I) species form very dark-colored mixed oxidation-state species with copper (II) species, when all iron (III) is used up. This causes the PCB-etchant liquid to turn very dark, when it is near exhausted.
You cannot simply say that copper is more noble than iron and so the reaction cannot proceed. This only is true for Fe(2+) and Cu. Fe(3+) is a more oxidizing ionic form of iron. With chloride ions present, the nobleness of copper is reduced, due to complex formation, as described above, and that effect makes Fe(3+) a sufficiently strong oxidizer to dissolve copper.
bottom of page